Major investments within the Defontaine Group
Between January 2021 and December 2023, the Defontaine Group carried out major investments supported by a 20% subsidy of the total financial investment from BPI France as part of the stimulus plan for industrial investment and modernization (France Relance).
Investments have enabled the company to upgrade its forging workshops for truck and aeronautical parts:
Acquisition of a 3D optical scanner from GOM, enabling the entire part to be scanned in 3D using a point cloud.
=> Detection of all defects, accurate scanning, time savings.
Installation of an electric furnace with automated loading in the aeronautical forge for expansion and rounding of parts, while guaranteeing uniform temperature.
=> Improved temperature management, increased load capacity for the expansion operation, reduced transfer times, improved working conditions.
Purchase of 2 numerically-controlled 4-roller rollers for the large forge to optimize the quality of forged blanks and reduce the number of operations.
=> La commande numérique permet de garantir une répétabilité du cintrage des pièces que nous n’avions pas avec le procédé manuel
- Mise en place d’un trolley, toujours pour la grosse forge permettant la modernisation de l’alimentation électrique des machines.
=> L’alimentation électrique se fait désormais avec un TGBT, soit un réseau d’alimentation moderne permettant important gain de sécurité.
- Acquisition d’une cellule robotisée d’ébarbage pour le meulage des soudures.
=> Digital control allows us to guarantee the repeatability of part bending that we didn’t have with the manual process.
Installation of a trolley, again for the large forge, to modernize the power supply to the machines.
=> The power supply is now provided by a TGBT, a modern power supply network offering significant safety gains.
Acquisition of a robotized deburring cell for weld grinding.
=> The automation of grinding operations is changing the blacksmith’s trade, eliminating the risk of RSI, and should enable us to reduce our raw material cross-sections thanks to better dimensional control of grinding operations.
The project was developed with GB2 Europe Technologie specifically for the needs of the Defontaine Group.
On the rolling machines: the small 4-roller rolling machine makes the truck forge safer, as it is capable of bending the blanks for the 2 forging lines, whereas we only had a single old machine for this operation.
Installation of a 2nd forging line: duplication of the 1st truck forging line with 2 notable differences:
- The use of a hydraulic press rather than a mechanical one
- A robot to load and palletize the part.
=> Less risk of breakage with a hydraulic press, more robust. Doubling of raw truck production. Fewer operators needed and less drudgery.
These investments were made between 2021 and the end of 2023. Other projects are in the pipeline outside the subsidy: vacuum oven, bar oven, welder modernization…
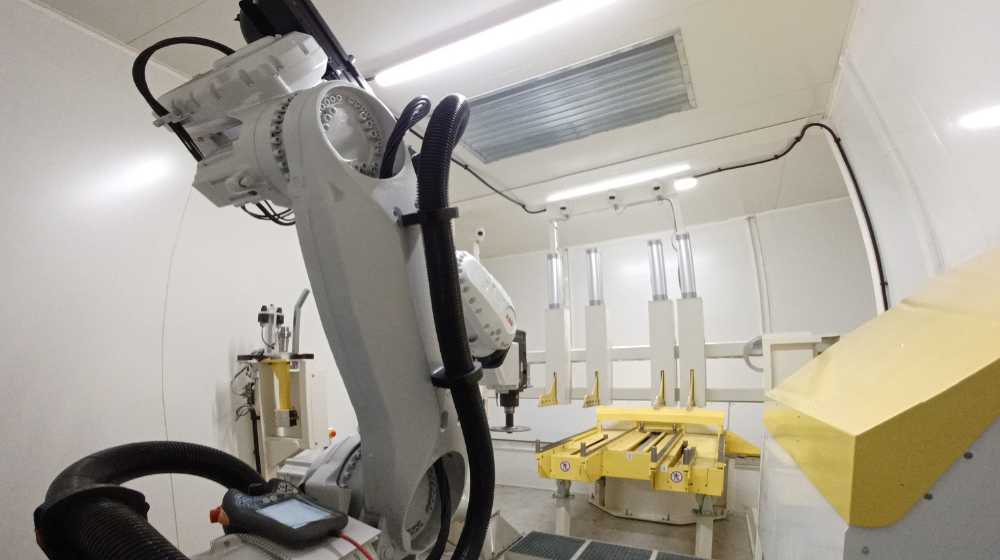
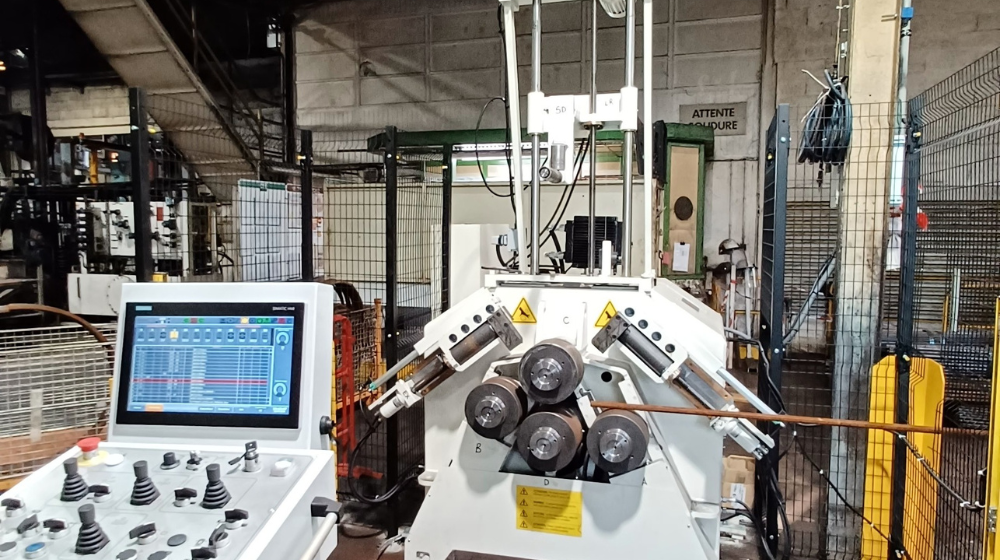
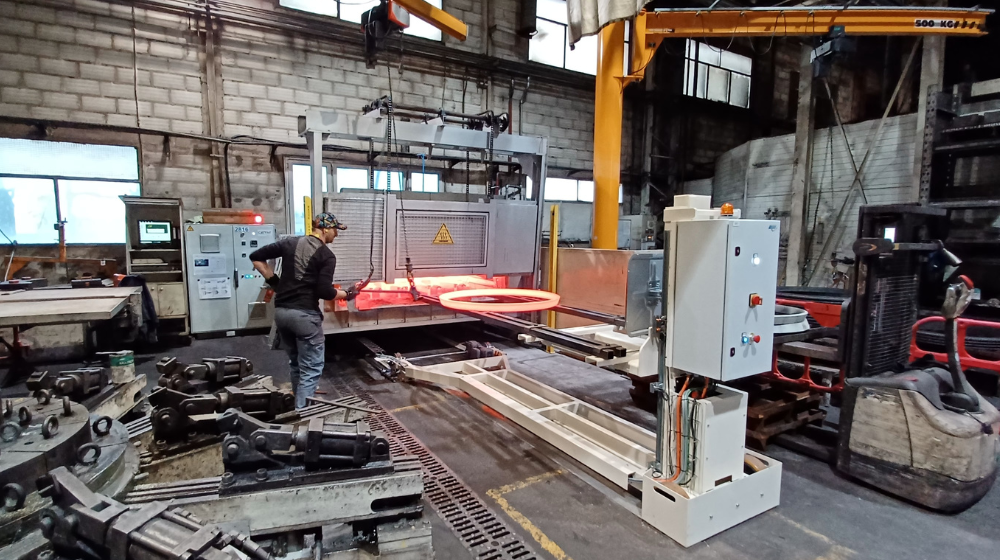