Our press quenching process
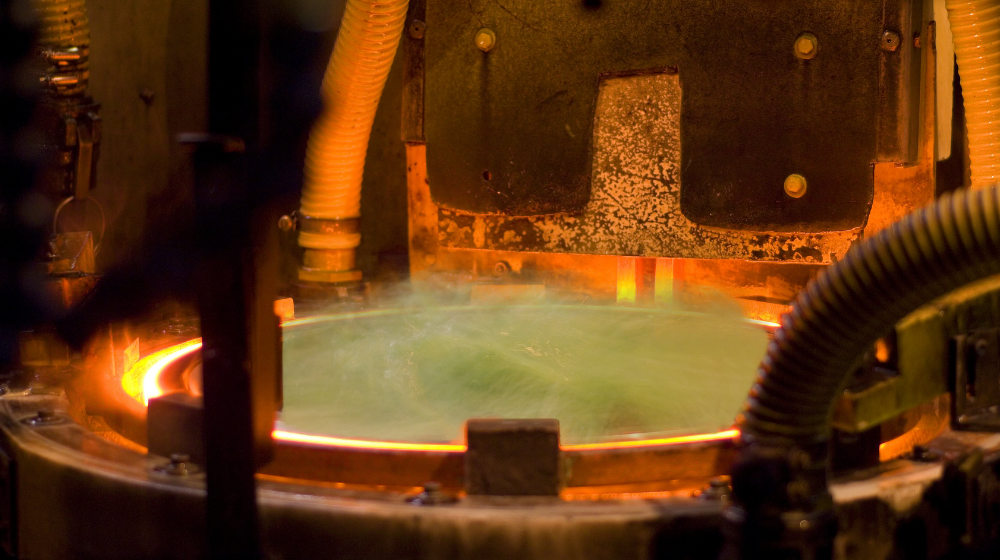
Press quenching is a heat treatment process used to harden metal parts. The principle is to heat a material until its internal structure changes and then cool it in a specific liquid, thus increasing its mechanical strength. This process combines heating and rapid cooling under controlled conditions.
To avoid the deformation caused by this heat treatment, Defontaine Group has used a technology that guarantees the dimensional conformity of the slewing ring during the heat treatment operation: press hardening. This specific process keeps the slewing ring under stress during the hardening phase, thus eliminating any risk of deformation and ensuring uniform hardening.
Therefore, we can highlight different steps in this process:
Heating
The metal part is heated to its austenitizing temperature, where its microstructure changes.
Pressing
After reaching the desired temperature, it is transferred to a quenching press. Afterward, mechanical pressure is applied to hold the part in the correct shape, ensuring it does not distort during cooling.
Quenching
Rapid cooling is then applied to the part while it is still under pressure to make the metal harden.
Final shaping
Press hardening ensures that the part retains its intended dimensions and shape throughout the cooling process to prevent warping or distortion.
This process also has various advantages:
- Dimensional accuracy: press hardening helps maintain tight tolerances and dimensional stability, which is critical for precision parts.
- Improved mechanical properties: the process enhances hardness, strength, and wear resistance.
- Reduced distorsion: by controlling the quenching process and applying pressure, the risk of warping and distortion is minimized, which is especially important for complex geometries.
Therefore, this specific process is vital to our industry to keep high-precision, strength and wear resistance for our products. It makes our products able to meet stringent specifications and performance criteria.
For more information about our processes, you can discover our flash-butt welding process in video: