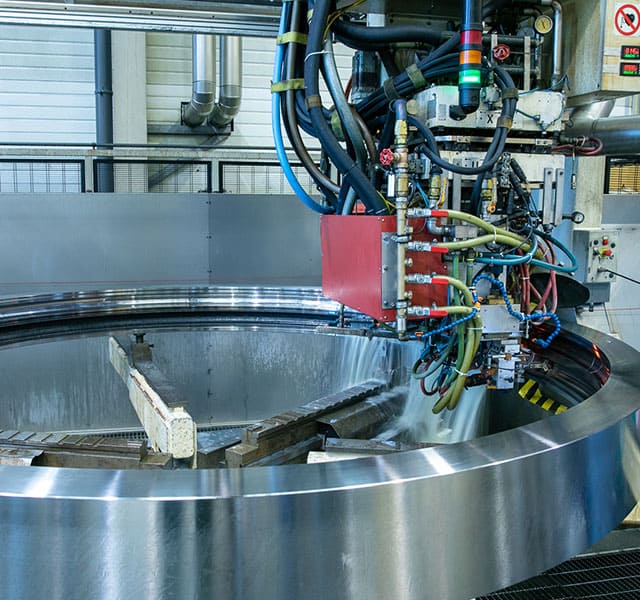
Our machine stock for state-of-the-art technology
- 5-axis machining centre
- Automated and robotic machining lines
- Flexible machining equipment for small and medium series, prototypes.
The Defontaine Group is the historical and reference partner of the precision industry. In order to meet the very high standards of our customers and their needs, we offer a wide range of controlled and customised solutions for the manufacture of rings in small series, large series and prototypes.
By machining, deformation or fusion processes, the Defontaine Group can help you define the best manufacturing processes according to the constraints your parts must withstand. Our proven expertise and know-how allow us to manufacture and deliver more precise, durable and reliable rings worldwide.
We have developed proven expertise in special processes, to ensure that our products meet the requirements of our customers.
“A special process is a process whereby the resulting output cannot be verified by subsequent monitoring or measurement, and, as a consequence, deficiencies become apparent only after the product is in use.”
Source: NADCAP
A so-called special process is a manufacturing process that is fully controlled by specifically qualified operators and for which the parameters are precisely determined and cannot be changed. The manufacture of a single part may require several special processes. Rollix bearings, for example, are both induction treated and MT inspected.
Discover all our other skills and trades
All our special processes are NADCAP certified
Surface or cylindrical grinding is a finishing machining process that aims to produce high-quality, high-precision metal parts in the micron range.
Grinding of the Rollix ring raceways guarantees the quality of the profile. This precision process also allows Defontaine Group to control the preload applied to our rings. Face and diameter grinding is also possible to reduce runout tolerances for high-precision parts.
Induction heat treatment or induction hardening is a non-contact heating system of metals, an electric current is induced in the part. This treatment increases the surface hardness and provides a better resistance to wear and tear against loads. All Rollix ring raceways are induction treated. Internal or external gear can also be treated if necessary.
Induction hardening is an efficient, economical and environment-friendly process which can achieve high hardening depths, process a large number of parts in a short period of time and does not require a vacuum atmosphere or the use of hazardous, polluting or chemical products.
Do you need special guidance?